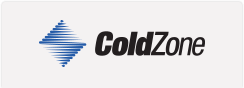
Q. What is a parallel compressor system?
A. Parallel compressor systems are made up of multiple compressors connected to a common suction manifold and discharge manifold. This type of system allows for greater capacities and the ability to meet more varying load conditions.
Q. The parallel compressor system came with an E2 RX-100 controller. What is it?
A. The E2 controller is a microprocessor-based control system designed to provide complete control of compres¬sor groups, condensers, refrigerated cases, and other com¬ponents related to refrigeration and building control. The E2 RX refrigeration controller uses the Enhanced Suction Group application to cycle compressors in an effort to maintain a constant suction pressure or temperature in a refrigeration system. A suction group may contain up to 16 compressor stages (standard, variable-speed, or unloader).
Q. How does the Enhanced Suction Group application work?
A. The Enhanced Suction Group application looks at suction pressure or suction temperature and compares it to the suction setpoint to determine whether compressor stages should be cycled ON or OFF. The Enhanced Suction Group keeps historical data of the effects each compressor stage has on the suction pressure or temperature, and analyzes that data to determine which stages to cycle. The Enhanced Suction Group application is designed to balance tight control of suction pressure with economic management of compressor cycling to reduce power usage and compressor wear.
Q. The E2 controller is asking for a Username and Password. What do I do?
A. Enter “USER” in the Username field and press the “Enter” key. Enter “PASS” in the Password field and press the “Enter” key. This provides Level 4 access which is the highest access level and allows the user to make changes to all the E2 functions. Logging into and out of the E2 controller can be done at any time by pressing the “Log In/Out” key on the E2 keypad. If you are currently logged out, pressing “Log In/Out” will bring up the User Login dialog box. If you are already logged in, pressing “Log In/Out” will immediately log you out and return you to the E2 home screen. For more information on creating Usernames and Passwords for different users refer to Section 10.12 Set UP User Access of the E2 Installation and Operation Manual.
Q. Why is there a USB flash drive inside the E2 controller?
A. We provide a USB flash drive loaded with various documents in PDF format and programming files with all our parallel compressor systems. The most useful document is the E2 Installation and User Manual. The USB flash drive also contains the factory program file for the E2 controller in case the program becomes corrupted or inadvertently changed. The program can be loaded into the E2 controller via the USB port located on the E2 controller by following the “Program Restore Instructions” document provided with the USB flash drive or can be downloaded from our website.
Q. How does the Copeland Scroll Digital™ modulate capacity?
A. The Copeland Scroll Digital operates in two stages — the “loaded state” and the “unloaded state”. Copeland Scroll Digital is equipped with an external solenoid valve. When the solenoid valve receives a 220V signal, the upper scroll moves up about one millimeter. This movement makes a gap between the orbited scroll and the fixed scroll; in addition there is no axial seal between these two scrolls. The compressor cannot compress the refrigerant even though the motor is still running. The capacity output is 100% in the loaded stage and 0% in the unloaded stage. The average capacity is a time-averaged summation of the loaded state and the unloaded state. For example, in a 20-second cycle time, if the loaded state time is 10 seconds and the unloaded state time is 10 seconds, the compressor modulation is 50% ((10 seconds x 100% + 10 seconds x 0%)/ 20).
Q. Do you have wiring diagrams, installation and operating information available? What about for older models?
A. Our Installation and Operations Manuals (IOMs) are available online and contain all the information needed to install, run and maintain our units. If you have an older model and can’t find the IOM online, use the Contact Form and provide us with the model and serial numbers and we’ll check our library and reply with the information.
Q. How can I determine the manufacture date of my unit?
A. We have an online HTPG Serial Numbers chart you can use to determine the facility, month and date of manufacture. You will need the full serial number of the unit. If the serial number of your unit has less than 18 digits, you’ll need to contact our ColdZone Customer Service Department at phone: 800-772-2653 and they can research it for you.
Q. Why does my freezer have icicles forming on the ceiling around the evaporator?
A. This problem is most often caused by excessive infiltration of moisture-laden air. Frequent door openings, air leaks, and heavy product loads can be primary causes. Our website has two documents that will be useful in correcting the problem: Icing in Walk-in Freezers and Systems Installation and Operations Manual.
Q. How can I replace the electric defrost heaters in my evaporator?
A. We have a bulletin that covers replacement of defrost heaters on our website: Defrost Heater Replacement.
Q. How can I determine the correct TXV for my evaporator if changing refrigerants?
A. We have a Sporlan Chart on our website for the preferred Sporlan Balanced Port TXV selections.
Q. What refrigerants do Coldzone products currently support?
A. Walk-in/warehouse style unit coolers as well as all air cooled condensers are available circuited for use with most any currently available HFC, HCFC (or even CFC) refrigerants. Most condensing units are available for use with currently available HFC’s, but can no longer be nameplated for use with any HCFC’s or CFC’s.
Q. What types of protective coil coatings are available for units which are installed in potentially corrosive environments?
A. Depending upon the product type, Coldzone currently offers three basic types of coil corrosion protection:
Q. Does Coldzone currently offer any of their products for use in explosion proof applications?
A. Although our products are sometimes modified in the field by other companies to conform to hazardous environments we do not offer any of our products in an explosion proof configuration as originally produced in our factory.
Q. What is the standard control voltage for Coldzone condensing units?
A. All condensing units are wired from the factory with 208/230 volt control circuit power. For 460 or 575 volt units this voltage is typically supplied from a factory mounted, step-down control circuit transformer. As an option, we offer 120 volt control power for most unit models for an additional cost.
Q. Where can I get submittal data sheets for the equipment I wish to order?
A. Submittal data sheets for many of our products can be found on our website on our Submittals page. If the unit model/ series which you require submittal data for isn’t listed, please contact your local ColdZone Sales Representative or use our Contact Form.
Q. How do I find my local ColdZone Sales Representative?
A. Our Find a Sales Representative tool will guide you.
Q. How do I find part numbers for replacement parts?
A. Contact ColdZone Customer Service by phone: 800-772-2653 or fax: 714-529-8503.
Q. Where do I obtain pricing for parts and equipment?
A. Contact your local sales representative.
Q. What is the availability for parts and equipment?
A. Contact your local sales representative for current availability.
Q. I received equipment which was freight damaged, what do I do?
A. Contact your local sales representative for proper direction and resolution.
Q. What are the Customer Service hours and how do I reach someone?
A. ColdZone Customer Service is open Monday – Friday from 7:00 a.m. – 4:00 p.m. Pacific Time. You can contact them at phone:
800-772-2653 or fax: 714-529-8503.
Q. How do I request a quote?
A. You can send your request via email to ColdZonequotes@htpgusa.com.
Q. How do I submit approval drawings or a Purchase Order?
A. You can send your request via email to ColdZonequotes@htpgusa.com.
Q. How do I track the shipment of my order?
A. After your order has been processed, you can track the shipment online. You’ll need your complete Purchase Order number or Order Number to track the shipment. If you don’t have the complete number, you can input part of the number and do a search to find the shipment. Please contact customer service personnel if you do not find your order listed or require more information regarding your shipment.
Q. Who do I contact to open an account?
A. You will need to contact your local ColdZone Sales Representative. He/she will provide the necessary paperwork to you to establish an account.
Q. How long will it take to establish an account?
A. It can take anywhere from one day to two weeks (worst case scenario) depending on how quickly we get responses from trade references.
Q. I haven’t purchased from you in quite some time. How do I reinstate my account?
A. If your account has gone inactive, we will need all new paperwork to reinstate the line. You will need to contact your local ColdZone Sales Representative to get the necessary paperwork.
Q. Will I be charged sales tax on my order?
A. We are registered to collect sales tax in all states. If you have your state exemption certificate, or the state you are drop shipping to will accept your home state exemption, then we will not have to charge tax.
Q. What is your remittance address?
A. 29946 Network Place, Chicago, Il 60673
Q. How do I submit a warranty claim?
A. Warranty submissions can be made via our claim submission form.
Q. Where do I go to get warranty replacement parts?
A. Please email the HTPG Parts Department at Parts@htpg.com for all replacement parts.
Q. What information do I need to submit an extended compressor warranty?
A. We need three things to process an extended compressor warranty:
By continuing to use this website, you agree to our use of cookies. For more information, see our Privacy Statement.